
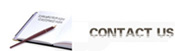
- Changchun Rongde Optics
- Co.,Ltd.
- Add:No.1666 Yaan Road,
- North Lake Development District,
- Changchun 130102,China
- Tel:86-431-81881745
- Fax:86-0431-85256892
- E-mail:rongdecui@roundss.net
- Skype:adacui_roundss
Application
Current position :Home > Application
Encoders Used in Industrial Robot!
China Changchun Roundss Optics Co.,Ltd. Release time:2015/1/6 Browse:6769
The robot rotary encoder can be used to improve a robot in various ways. The robot shaft encoder can measure rotational distance traveled and speed, which can be used to monitor, for example, the angular position of a robot gripper arm or the speed of a robot. Knowing these parameters can greatly assist you with performing autonomous tasks with your robot.
The robot quad motor encoder can be used to track distance traveled, direction of motion, or position of any rotary component, such as a gripper arm. The robot wheel encoder can also be used to detect movement, which could facilitate richer interaction between the robot and its environment (e.g., human-robot interaction). If a human moves a robot arm that is attached to an motor encoder (e.g., during a handshake), the robot detects the arm movement and the direction(s) and distance(s) traveled, helping the robot classify the interaction as a handshake.
Photoelectric encoder is a widely used position sensor with a high resolution which can meet the technical requirements of the robot. This non-contact sensor can be divided into absolute encoder and relative encoder(Incremental encoder). The absolute encoder could supply the actual encoder linear or rotational position, can be given by the actual linear or rotational position as long as power is applied to such a sensor in the electromechanical system. Thus, the robot joints equipped with absolute encoder does not require calibration equipment. a, the controller will know the actual joint positions when connected with power. Relative encoder (Incremental encoder)only provide a reference point corresponding to the location information obtained. Therefore, the calibration process should be completed before the relative encoders obtain the true position of the robot.
Roundss Encoder(Changchun Rongde Optics Co.,Ltd) supply both absolute encoders and incremental encoders to meet your different requirements.
For robot industry application, small and compact encoders are recommended to suit the small mounting place of the robotic arm.
Roundss' complete product line of Small Solid Shaft and Hollow Shaft encoders have always used for robot applications. The small Rotary Encoder Series RCC25S and RCC30S are the primary encoders requested by the robot arm with shaft diameters ranging from 4mm. The Reinforced type DCC25S and DCC30S with higher protection Class IP 65 are available in resolution from 20 to a maximum of 1200 ppr.
Roundss product line includes Incremental and Absolute Encoders from 4 to 15 mm in diameter and with shaft bores up to 45mm in diameter. Roundss' products have been proven and used extensively in Robots, Cranes, Forestry, Oil and Gas, Machining, Elevator, Factory Automation and Food Processing, and Energy Production applications. Roundss is also certified to CE standards.
Previous:None!
Next:Encoders for Elevator Application