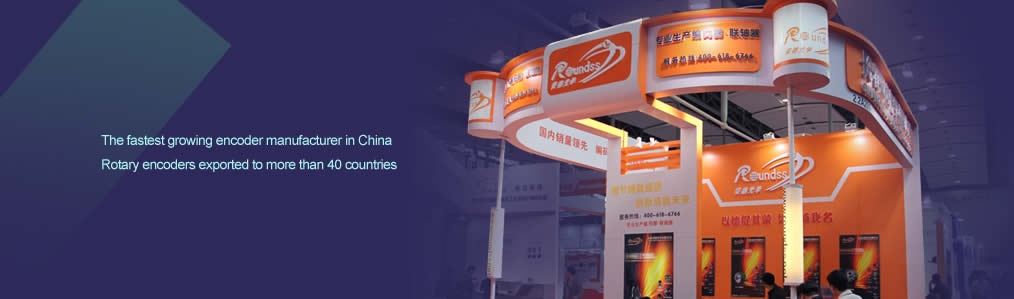
Roundss News
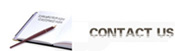
- Changchun Rongde Optics
- Co.,Ltd.
- Add:No.1666 Yaan Road,
- North Lake Development District,
- Changchun 130102,China
- Tel:86-431-81881745
- Fax:86-0431-85256892
- E-mail:rongdecui@roundss.net
- Skype:adacui_roundss
Company News
Current position :Home > News > Industry News
Rotary optical encoder design trends2!
Changchun Rongde Optics Co.,Ltd. Release time:2016/7/23 Browse:1480Rotary optical encoder design trends
Photoelectric encoder is a mechanical motion control measure rotational body position (angle) and speed sensor, it has two kinds of rotary and linear, wherein the rotary optical encoder due to high precision, easy installation, has been widely used. With the rapid development of motion control products, China's demand for high-precision encoders big, but mainly rely on imports. Currently, active in the market of the encoder is mainly foreign, such as Germany Heidenhain (Heidenhain), Mel (Meyle), Fuchs (P + F), Turck (Turck), USA (GPI), Japan Tamagawa, Renishaw (Renishaw), Korea (Metronix), Autonics (Autonics), Fort Union, Switzerland (Baumer), Turkey (OPKON), as well as our CIMIC like. Throughout recent years, rotary optical encoder of development, its design trends include the following four aspects to elaborate.
Second, optimize the product structure.
Rotary optical encoder by the optical path, circuit and mechanical components 3, the encoder manufacturer attaches great importance to the three parts of the design and production.
(1) optical systems: one LED light source shining diode, optical focusing system design, the LED emitted light becomes a parallel beam is irradiated perpendicularly to the rotary encoder (dynamic grating) and the fixed code disk (fixed raster) on after passing through the two slits light transmissive code wheel light is absorbed by the photodiode output signals to analog conversion circuit for signal processing. Since the optical system of the smoke, dust, water vapor, and other very sensitive to mechanical vibrations, all ships are designed to strict protective measures, the highest level of protection currently an optical rotary encoder is designed around IP65, the maximum operating temperature of about 85 ℃. Second encoder selection of materials, glass, plastic, stainless steel, has been adapted to different needs, including high glass code disc precision, good thermal stability, but resistance to vibration difference; accuracy and thermal plastic and stainless steel stabilized somewhat less, but resistance to vibration low cost plastic, can be made economical. Grating encoder on the general use of the deposition of thin engraved lines (such as glass code disc), mechanical scribing or photolithography production. Third, the design of the grating, incremental and absolute completely different. Incremental (quadrature) encoder: rotary encoder edge portion of the radial slit translucent design has many uniformly distributed, their width and spacing equal to its number of light-transmitting slit design and processing quality will directly affect the encoder measurement accuracy; on the fixed code disk has a, B, Z three slits (rotating code wheel has a gap corresponding to the Z), a, B two quadrature output (electrical angle difference of 90 °) of square wave pulse signal, the calculation for the measured motor speed, position (angle) and the steering discrimination; Z-phase signal is used as reference mark, sending a pulse per revolution for the motor rotor position, the cumulative number of revolutions. Absolute encoder: n-bit absolute encoder on the rotary encoder on the design of concentric circles of n code channel, using pattern Gray (GRAY) Code design, code wheel from the edge to the center of the track n barcode, translucent the number of sectors by 20,21,222n-1 design, production; only radial slits on a light-transmissive code wheel is fixed, corresponding to each code channel behind a photodiode, an n-bit digital output code (Gray code can be converted binary code or BCD code) represents the absolute position of the shaft at a time, especially for monitoring the shaft position during power-up and power-down. This encoder has been adopted most manufacturers design pattern when Gray code, because it is only one digit changes between two adjacent numbers, the error is small; if the binary pattern, although its design is simple, but the production, installation is very strict, or prone to double-digit error.
(2) circuit section: includes an encoder main circuit and output circuit. Photodiode output signal level is low, the waveform is not the rule, in order to control, information processing and remote transmission, subject to the conversion circuit Fat, shaping. Previous switch circuit design using discrete components, spare parts and more complex structure, expensive price. Now there are many manufacturers such as Fuchs and other main circuits into an application specific integrated circuit (ASIC), using ASIC design, not only interference, resistance to changes in environmental conditions, to improve the detection accuracy and speed, but also due to reduced parts, structure compact and simple, so that the absolute encoder prices, According to reports, the general price than the old models about 20%. Output circuit in many forms, Metronix other companies designed five types: open collector output, voltage output, push-pull output line driver outputs complementary output. To reduce noise, improve the reliability of the output, can be used push-pull or complementary output; when you need long-distance transmission, the available line driver output or complementary output. In practice, a little machine or production line required dozens encoder connected to a distributed control, the new encoder circuit section is also designed to set the address switch encoder, the host controller at any time to facilitate accurate To read information from the encoder.
(3) Mechanical parts: With the increasing speed of the servo motor, encoder design generally considered able to withstand the maximum speed, the current general maximum speed of 6000r / min, while Turck encoder 12000r / min, highlights its shaft and bearing thermal design optimization techniques. Usually encoder uses stainless steel shaft and high-precision bearings, shaft with solid, hollow and through-type, easy to deal with a variety of application needs. The encoder housing is generally made of high strength aluminum (OPKON company uses an oxygen electrode alumina).
In addition, optimize the product structure design, most manufacturers also particularly concerned about the size, weight and tightness. For example, the output shaft and cable connections are sealed two weak links, Lost Horizon (Tianjin) Company uses advanced shaft seal, seal design at Fuchs cable connections reaches protection class IP67.
Photoelectric encoder is a mechanical motion control measure rotational body position (angle) and speed sensor, it has two kinds of rotary and linear, wherein the rotary optical encoder due to high precision, easy installation, has been widely used. With the rapid development of motion control products, China's demand for high-precision encoders big, but mainly rely on imports. Currently, active in the market of the encoder is mainly foreign, such as Germany Heidenhain (Heidenhain), Mel (Meyle), Fuchs (P + F), Turck (Turck), USA (GPI), Japan Tamagawa, Renishaw (Renishaw), Korea (Metronix), Autonics (Autonics), Fort Union, Switzerland (Baumer), Turkey (OPKON), as well as our CIMIC like. Throughout recent years, rotary optical encoder of development, its design trends include the following four aspects to elaborate.
Second, optimize the product structure.
Rotary optical encoder by the optical path, circuit and mechanical components 3, the encoder manufacturer attaches great importance to the three parts of the design and production.
(1) optical systems: one LED light source shining diode, optical focusing system design, the LED emitted light becomes a parallel beam is irradiated perpendicularly to the rotary encoder (dynamic grating) and the fixed code disk (fixed raster) on after passing through the two slits light transmissive code wheel light is absorbed by the photodiode output signals to analog conversion circuit for signal processing. Since the optical system of the smoke, dust, water vapor, and other very sensitive to mechanical vibrations, all ships are designed to strict protective measures, the highest level of protection currently an optical rotary encoder is designed around IP65, the maximum operating temperature of about 85 ℃. Second encoder selection of materials, glass, plastic, stainless steel, has been adapted to different needs, including high glass code disc precision, good thermal stability, but resistance to vibration difference; accuracy and thermal plastic and stainless steel stabilized somewhat less, but resistance to vibration low cost plastic, can be made economical. Grating encoder on the general use of the deposition of thin engraved lines (such as glass code disc), mechanical scribing or photolithography production. Third, the design of the grating, incremental and absolute completely different. Incremental (quadrature) encoder: rotary encoder edge portion of the radial slit translucent design has many uniformly distributed, their width and spacing equal to its number of light-transmitting slit design and processing quality will directly affect the encoder measurement accuracy; on the fixed code disk has a, B, Z three slits (rotating code wheel has a gap corresponding to the Z), a, B two quadrature output (electrical angle difference of 90 °) of square wave pulse signal, the calculation for the measured motor speed, position (angle) and the steering discrimination; Z-phase signal is used as reference mark, sending a pulse per revolution for the motor rotor position, the cumulative number of revolutions. Absolute encoder: n-bit absolute encoder on the rotary encoder on the design of concentric circles of n code channel, using pattern Gray (GRAY) Code design, code wheel from the edge to the center of the track n barcode, translucent the number of sectors by 20,21,222n-1 design, production; only radial slits on a light-transmissive code wheel is fixed, corresponding to each code channel behind a photodiode, an n-bit digital output code (Gray code can be converted binary code or BCD code) represents the absolute position of the shaft at a time, especially for monitoring the shaft position during power-up and power-down. This encoder has been adopted most manufacturers design pattern when Gray code, because it is only one digit changes between two adjacent numbers, the error is small; if the binary pattern, although its design is simple, but the production, installation is very strict, or prone to double-digit error.
(2) circuit section: includes an encoder main circuit and output circuit. Photodiode output signal level is low, the waveform is not the rule, in order to control, information processing and remote transmission, subject to the conversion circuit Fat, shaping. Previous switch circuit design using discrete components, spare parts and more complex structure, expensive price. Now there are many manufacturers such as Fuchs and other main circuits into an application specific integrated circuit (ASIC), using ASIC design, not only interference, resistance to changes in environmental conditions, to improve the detection accuracy and speed, but also due to reduced parts, structure compact and simple, so that the absolute encoder prices, According to reports, the general price than the old models about 20%. Output circuit in many forms, Metronix other companies designed five types: open collector output, voltage output, push-pull output line driver outputs complementary output. To reduce noise, improve the reliability of the output, can be used push-pull or complementary output; when you need long-distance transmission, the available line driver output or complementary output. In practice, a little machine or production line required dozens encoder connected to a distributed control, the new encoder circuit section is also designed to set the address switch encoder, the host controller at any time to facilitate accurate To read information from the encoder.
(3) Mechanical parts: With the increasing speed of the servo motor, encoder design generally considered able to withstand the maximum speed, the current general maximum speed of 6000r / min, while Turck encoder 12000r / min, highlights its shaft and bearing thermal design optimization techniques. Usually encoder uses stainless steel shaft and high-precision bearings, shaft with solid, hollow and through-type, easy to deal with a variety of application needs. The encoder housing is generally made of high strength aluminum (OPKON company uses an oxygen electrode alumina).
In addition, optimize the product structure design, most manufacturers also particularly concerned about the size, weight and tightness. For example, the output shaft and cable connections are sealed two weak links, Lost Horizon (Tianjin) Company uses advanced shaft seal, seal design at Fuchs cable connections reaches protection class IP67.
Previous:Rotary optical encoder design trends3
Next:Rotary optical encoder design trends