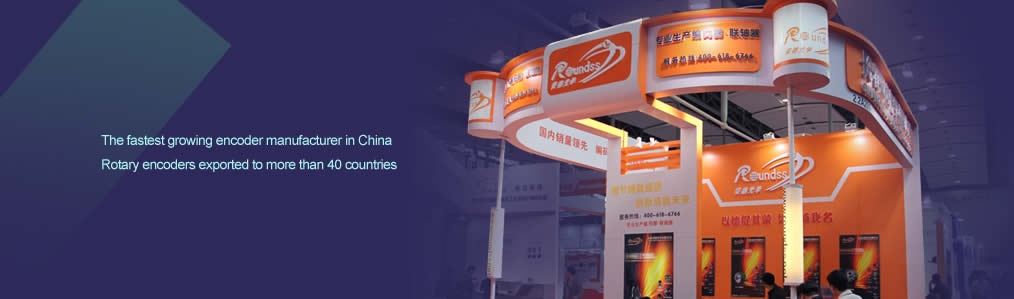
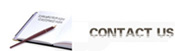
- Changchun Rongde Optics
- Co.,Ltd.
- Add:No.1666 Yaan Road,
- North Lake Development District,
- Changchun 130102,China
- Tel:86-431-81881745
- Fax:86-0431-85256892
- E-mail:rongdecui@roundss.net
- Skype:adacui_roundss
Company News
Current position :Home > News > Photoelectric Sense
Encoders-absolute encoders/ incremental encoders!
Changchun Rongde Optics Co.,Ltd. Release time:2017/9/23 Browse:1158Encoders
A Rotary encoder,which also known as a shaft encoder, is an electro-mechanical device that converts the angular position or motion of a shaft or axle to an analog or digital code.There are two main series of encoders: absolute and incremental (relative). The output of absolute encoders indicates the current position of the shaft, making them angle transducers. The output of incremental encoders provides information about the motion of the shaft, which is typically further processed elsewhere into information such as speed, distance, RPM and position.Rotary encoders are used in many applications that require precise shaft unlimited rotation—including industrial controls, robotics, special purpose photographic lenses, computer input devices (such as optomechanical mice and trackballs), controlled stress rheometers, and rotating radar platforms.
For Distances, positions and angles — when precise positioning is required, Roundss Encoder is unbeatable. For distance measurement applications, the resolution of the encoder is in the micrometer range, and when making angular measurements, it is equivalent to a few thousandth degrees. Our line includes absolute, non-contact length measuring systems, wire-draw encoders and compact measuring wheel encoders.
Rotary Incremental Encoders
Rotary encoders are often used to track the position of the motor shaft on permanent magnet brushless motors, which are commonly used on CNC machines, Industrial robots, and other industrial equipment. Incremental (Quadrature) encoders are used on Induction Motor type servomotors, but absolute encoders are used in Permanent Magnet Brushless Motors, where applicable. In these applications, the feedback device (encoder) plays a vital role in ensuring that the equipment operates properly. The encoder synchronizes the relative rotor magnet and stator winding positions to the current provided by the drive. Maximum torque results if the current is applied to the windings when the rotor magnets are in a particular position range relative to the stator windings. The motor will perform poorly or not at all if this timing is not adjusted correctly. Improper encoder alignment on the motor can actually cause it to run backwards sometimes resulting in a hazardous run away condition. Correct alignment is essential to proper operation of these motors.
Absolute Encoders
Every Absolute Rotary Encoder is used to determine the speed or position of something – the difference is in how that encoder determines that movement. Absolute encoders work in situations where accuracy for speed and position, fail tolerance, and interoperability matters more than system simplicity.
An Absolute Rotary Encoder determines its position using a static reference point. The method is slightly different depending on whether the absolute rotary encoder is optical or magnetic, but the principle is the same either way.
By having an integrated reference, an absolute rotary encoder is intrinsically able to deliver higher quality feedback:
Features
· Extremely robust, tried-and-tested absolute multiturn encoder with a resolution of up to 26 bits
· Mechanical interface: Through hollow shaft with shallow installation depth
· Zero-set and preset functions via hardware or software
· No battery required
· Electrical interface: SSI with gray or binary code type
· Electronically adjustable, configurable resolution
· Magnetic scanning
· Higher overall resolution and orientation
· Better start up performance because of low homing (or initial position) time
· Accurate motion detection along multiple axes
· Multiple output protocols for better electronics integration
· Better recovery from system or power failures
Previous:What is the use of servo motor encoder?
Next:Encoders Used in Industrial Robot!