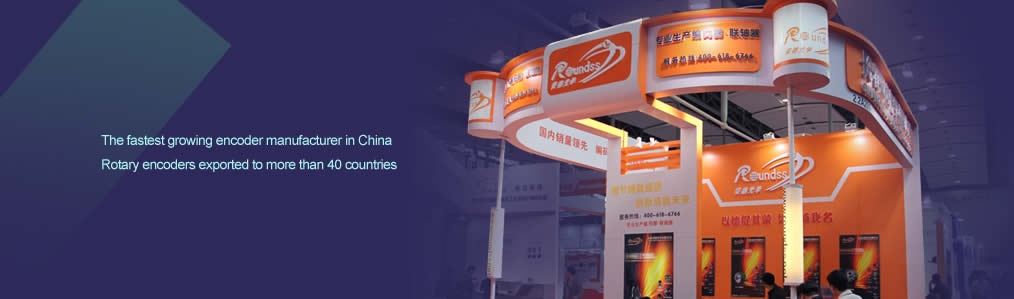
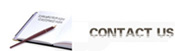
- Changchun Rongde Optics
- Co.,Ltd.
- Add:No.1666 Yaan Road,
- North Lake Development District,
- Changchun 130102,China
- Tel:86-431-81881745
- Fax:86-0431-85256892
- E-mail:rongdecui@roundss.net
- Skype:adacui_roundss
How to get motor feedaback by encoder?!
Changchun Rongde Optics Co.,Ltd. Release time:2017/11/15 Browse:1225There are many ways to get feedback on DC motor motion. People who control the system tend to leave a mark on the motor shaft or "tape" the tape so they can visually see the shaft turning. This helps to ensure that the direction of the movement is correct (otherwise the DC polarity reversal is required). It also helps to observe movement at low speeds - but otherwise not suitable for automated systems.
If you want to automatically observe the rotation of the motor, you must use some type of sensor to provide the control computer with the appropriate information. There are many ways to do this. For example, it is possible to monitor the current draw of the motor windings and use the motor constant kτkτ to infer the torque produced by the motor. This accelerates the axis by using the appropriate system dynamics model. However, this method is not very accurate, and prone to simulation error and signal noise. This method is similar to monitoring PWM outputs and inferring motion dynamics - neither can change the dynamics of the system. Another method is to affix the magnet to the shaft and monitor it with a Hall effect sensor. This will provide one pulse per revolution of the motor. This is usually a solution for high temperature or dirty environments, such as in automotive applications. However, more granular motion is usually required. This is where the encoder comes in.
There are two basic types of encoders: incremental and absolute. They can be further characterized as orthogonal or non-orthogonal encoders. Non-quadrature incremental encoders provide a pulse to the controller for each incremental movement of the motor shaft. As shown in the previous answer, this positional feedback can be interpreted as inferring velocity, acceleration, and possibly jerkiness (although the three derivatives of the sensed value are "spikey" in most applications). However, this type of encoder provides information only when the position is changed, and does not provide any information about the direction of movement. Quadrature encoders provide two out-of-phase pulses and can also be used to detect the direction.
Absolute encoders not only provide the same information as incremental encoders, but also provide more bits of information about the angular position of the shaft and the incremental changes in position.
You can make a very simple encoder using a slotted disc. Place a photodiode on the side of the disc and a photodetector on the other side. You get a pulse each time you insert a slot between the sensor elements. As you can see, the accuracy of motion detection is determined by the number of slots in the disc. The encoder can provide many different numbers of pulses per revolution.
Previous:Open Loop vs. Closed Loop
Next:How I can choose my manual pulse generator?